Almost
a Hundred White Oak Barrels Revitalized
Whiskey
barrels finish their role after 50 to 70 years.
Most of the barrels are made of white oak, as firm
as to be employed as the hull material for battleships
in Victorian Age. White-oak trees were under strict
control in growing and felling at that time and
regarded as "the king of forest" in England.
The wood of the barrels used for re-building MALT'S
MERMAIDIII are cut from 150`300 years old
native white-oak trees that grow on Mississippi
River valley, and is said to last almost forever,
the most sufficient material for the whiskey barrels.
Almost a hundred barrels having completed their
role, are recycled as white-oak hull of MALT'S MERMAIDIII.
This wood is not only firm but is also straight-grained,
an extravagant usage of wood in order to avoid the
leaking of the liquor.
We believe that using wood as long as possible will
reduce the number of trees being cut and save the
forests in consequence. We hope to promote the idea
of treasuring wood through revitalizing the used
barrels as a ship and showing them play a new role.
Plywood Recycling White
Oak
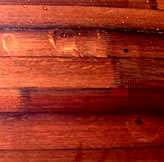 |
White
oak of whiskey barrels needs to be reformed before
utilized. Recycling the planks starts from straightening
the curve that is unique to barrel planks. The reformed
planks are then planed until they are even, consequently
leaving only 20`30% of the gross.
Combining the reformed boards, blocks in two sizes
of 500mm by 200mm by 2.7m and 150mm by 200mm by
1.2m are formed. 1.2mm thick sheets are grated from
the formed blocks, then glued together vertically
then horizontally on the other in layers until they
are 6mm (5 layers) or 9mm (7 layers) thick.
How to straighten the curved plank was already applied
in reforming wood to furniture in "White Oak Furniture"
series by soaking them in hot water and sparing
them. But making them into plywood, especially grating
flat sheets of wood of 1.2mm thick was quite an
assignment. As the behavior of plywood is strongly
influenced by the glue, much effort was paid to
find the adequate glue for the firmness and the
flexibility of the plywood.
Gluing the sheet in layers had to be done carefully
by hand, one by one, accomplishing only one board
a day, hence attaining supreme plywood in strength
and workability. |